The Rotomoulding process uses plastic powders. Key stages are:
- colouring of the plastic powder by adding colouring agents and dosing the coloured material to suit the required final weight for the part
- loading the material to the rotomoulding system and closing it
- slowly rotating the mould on two axes while heating
- cooling the mould
- removal from the mould
Colouring and dosing:
The colouring step employs a turbomixer, cement mixer or compounding.
Compounding is the most reliable solution for thorough mixing of the colouring agent and plastic. This is a hot mixing method, in which the plastic is kneaded with the colouring agent in a compounding screw.
The turbomixer is a solution which uses both the mechanical action of the blades on the material, and the heating action arising from friction during the process.
A cement mixer is the simplest and cheapest solution, giving highly satisfactory results in 80% of applications.
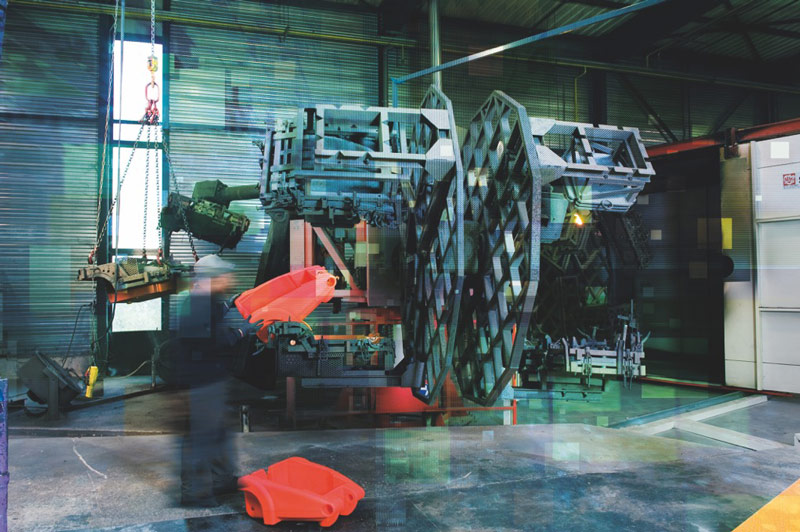
Arrangement of the material in the mould, closing of the mould:
The previously coloured dosed material is poured into the mould using an adapted (or another) container. This operation requires great care by the operator, to leave joint line areas clean. The operator then closes the mould. Some moulds use clamps, others a screw. Design of the ergonomic aspects of the mould is particularly important for productivity – each mould requires careful consideration for the design of its closure.
Applications
The numbers of rotomoulding applications are constantly increasing and are generally small- or medium-scale. The moulds are not expensive (compared to injection moulds) once we take into account the size of the parts to be rotomoulded, allowing small runs to be produced cost-effectively. Rotomoulding solutions are also quick to deliver and do not generally require complex development.
Rotomoulded parts are used for the following:
- specialty machines – hoods, fairings
- specialty and non-licensed vehicles – internal fittings
- industry – packaging solutions
- tanks and vessels
- traffic signals – lane markings, boards
- maritime applications – beacons, pontoons
- leisure – fitness, floating craft
Rotomoulded materials
Polyolefins are by far the materials most used for rotomoulding (PP, HDPE), though PVCs (solid or liquid) still account for a significant proportion and new plant-based materials are emerging (PLA).