Généralités et principe du thermoformage :
Le thermoformage est une technologie de transformation et de mise en forme des matières plastiques polymères. Il permet de réaliser des pièces de petites dimensions comme des pièces de plusieurs mètres carrés. La technologie de thermoformage s’est développée à partir des années 60 en parallèle du développement des matières plastiques.
Il en existe plusieurs dont l’extrusion, l’extrusion-soufflage, la chaudronnerie, le calandrage, la thermo pression, l’injection, l’injection soufflage, le moulage par réaction RIM, le rotomoulage ou encore le soudage.
Le thermoformage fine épaisseur est réalisé à partir de bobines de matières plastiques dont l’épaisseur est inférieure à 2mm pour des applications type emballages alimentaires ou conditionnements perdus. Le thermoformage forte épaisseur est quant à lui réalisé à partir de plaques ou de feuilles rigides extrudées avec des épaisseurs généralement supérieures à 2 mm, et il est destiné à des applications de cartérisation par exemple ou de conditionnements retournables.
Le principe du thermoformage consiste à chauffer la plaque de plastique pour la ramollir, faire le vide entre la plaque ramollie et l’outillage, puis de la refroidir pour obtenir une forme tridimensionnelle.
Les étapes du thermoformage :
Le cycle de thermoformage classique se compose de plusieurs étapes :
La fixation de la plaque :
La fixation de la plaque sur un cadre peut être manuelle ou automatisée en fonction du type de machine.
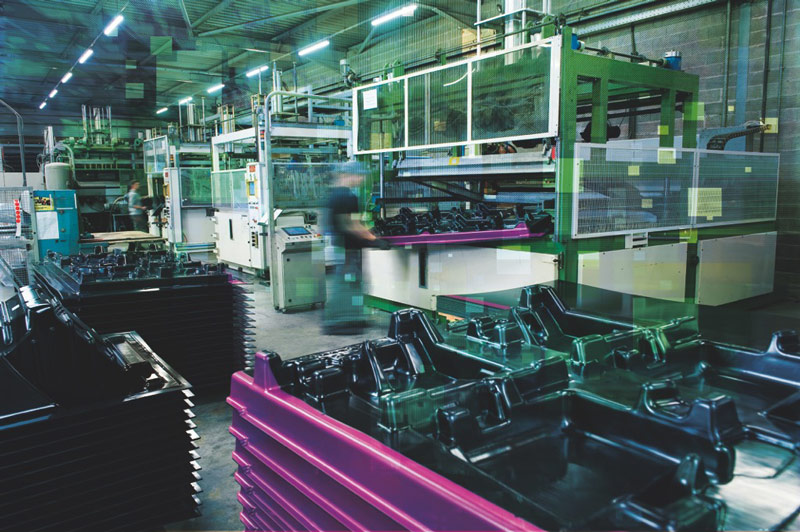
Le chauffage de la feuille de plastique :
Il existe différents types de chauffes :
- par radians
- par infrarouge
- par halogènes
Le chauffage est généralement assuré par deux panneaux chauffants, un supérieur et un inférieur, constitués de résistances. Ces panneaux chauffent la matière en sandwich. Cette dernière est maintenue en position horizontale par une légère surpression, ce qui lui évite de s’affaisser.
Les temps de chauffes sont très variables, et dépendent du type de matière, de sa couleur mais également de l’épaisseur de la matière plastique, pouvant aller de quelques secondes (pour des épaisseurs de quelques dixièmes de mm) à plusieurs minutes (pour des épaisseurs de quelques mm). Il est nécessaire de dépasser la température de transition vitreuse des polymères Tg et de chauffer à cœur les matériaux.
Le formage de la plaque par aspiration :
Une dépression par le vide est faite entre l’outillage et la feuille de plastique ramollie via les trous d’aspiration sur l’outillage. Ces orifices sont de petits diamètres (entre 0,5 et 1mm) et sont positionnés stratégiquement sur l’outillage. Ils servent à évacuer l’air enfermé entre la plaque et l’outillage. Ces perçages sont reliés à une pompe à vide, qui se déclenche au moment de la phase de formage. Le vide est généralement de 0,1 bar. Cette phase dure de quelques dixièmes de secondes, à quelques secondes, selon les épaisseurs et les contraintes de formage.
Le thermoformage en positif permet une gestion des formes et des cotes intérieures de la pièce. Les cotes extérieures dépendent donc de l’épaisseur de départ de la plaque et de l’étirement de la matière. Un minimum de dépouille de l’ordre de 1,5° est nécessaire pour assurer le démoulage car le retrait thermique du plastique peut serrer la pièce sur le moule et provoquer des difficultés de démoulage.
Le thermoformage en négatif, quant à lui, permet une gestion des formes et des cotes extérieures de la pièce. Les cotes intérieures dépendent donc de l’épaisseur de départ de la plaque et de l’étirement de la matière. Le thermoformage en négatif peut permettre d’avoir des faces sans dépouille.
Il est possible également de s’aider par de l’air comprimé pour faciliter les formages complexes.
Généralement, un bullage (étirage de la matière avant formage) est effectué pour avoir un étirement matière le plus homogène possible et éviter l’emboutissage de la matière et donc des épaisseurs non homogènes.
Afin de maitriser l’étirement de la matière, il est possible d’utiliser un poinçon. La feuille touchée par le poinçon se refroidit localement et son élasticité diminue.
De même que pour une bonne répétabilité et une homogénéité dans le dimensionnel des pièces, il est préférable d’utiliser des moules régulés en température par le biais d’une circulation de fluide dont la température est contrôlée via un thermorégulateur.
Les moules peuvent être de différents matériaux, bois ou résine pour de petites séries et en aluminium usiné ou fonderie d’aluminium pour la série.
Le refroidissement de la forme tridimensionnelle :
Le refroidissement peut être obtenu par simple ventilation (ce principe est le moins cher, mais aussi le moins efficace). Plus généralement le refroidissement est obtenu par une circulation de liquide réfrigéré dans le moule.
Le démoulage :
Il peut se faire soit naturellement, soit en utilisant les canaux d’aspiration pour souffler de l’air et donc aider la forme à se démouler.
L’outillage est monté sur une platine guidée par un vérin sur un axe vertical et descend pour libérer la pièce.
La découpe :
Il est déjà nécessaire dans un premier temps de séparer la pièce du reste de la feuille de plastique restante afin d’éviter les contraintes résiduelles liées notamment aux bandes froides qui sont les zones non chauffées situées dans le serre-flan.
Les différentes techniques de découpe sont, le poinçonnage, le sciage, l’usinage par commande numérique, la découpe laser, la découpe jet d’eau…
Le thermoformage et ses avantages :
Le thermoformage est une technologie employée pour réaliser des pièces techniques, esthétiques et complexes, de la cartérisation, mais également du conditionnement spécifique, de l’emballage, des plateaux de manutentions et de l’équipement de bord de lignes notamment pour le secteur automobile.
Le temps de développement est relativement cours et est d’environ 8 à 10 semaines avec des coûts d’outillage abordables, moins importants que l’injection plastique par exemple.
Le thermoformage permet de réaliser différentes références de pièces à partir d’un même outillage en changeant la couleur des pièces par exemple mais également en modifiant la découpe faite dans un second temps. Il existe un panel de matières important avec des caractéristiques et propriétés variées permettant de répondre à toutes les contraintes et applications demandées par nos donneurs d’ordres.
Les matières transformées :
Les principales matières transformées sont des matières simples comme les styréniques, les polyoléfines, les méthacryliques, mais également des matières complexes comme des compounds ou des coextrusions.
Le thermoformage permet de transformer une large gamme de matériaux thermoplastiques opaques, transparentes, diffusantes, fumées ou classées au feu comme :
- Opaques : ABS, ABS PMMA, ABS ASA, ABS PC, ABS TPU, PS, PP, PEHD, PVC, PS PE, PMMA, ASA…
- Transparentes : PC, PETG, APET, PVC, PMMA…
- Diffusantes : PETG, PC, PMMA…
- Fumées : PETG, PC, PMMA…
- Classées au feu : PC, ABS UL94HB (horizontal burning) ou VB (vertical burning)…, PETG, PVC, KYDEX, ABS PC, matières spéciales répondant aux normes aéronautiques ou ferroviaires
( ABS = Acrylonitrile-Butadiène-Styrène; PS = PolyStyrène; PC = PolyCarbonate; PETG = Polyester, PolyEthylène Théléphtalate amorphe; PVC = PolyChlorure de Vinyle; PMMA = PolyMétAcrilate de Méthyle; ASA = Acrylonitrile-Stryrène-Acrylester; PEHD = PolyEthylène Haute Densité; PP = PolyPropylène )
Certaines matières peuvent absorber de l’humidité avant thermoformage et générer après formage des défauts d’aspects liés à l’évaporation de l’humidité présente dans les plaques. Pour éviter cela, un passage en étuve permet de sécher les plaques. Le temps d’étuvage dépend du type de matière, de l’épaisseur des plaques et de l’âge et des conditions de stockage de celles-ci.
Les plaques de plastique sont teintées dans la masse. On peut avoir des nuances de couleurs type RAL ou pantone, voire du contretypage avec des aspects de surfaces lisses ou texturées. La texture est obtenue par le cylindre graineur lors du processus d’extrusion.
Sur les matières lisses, il est possible d’avoir un film de protection transparent en polyéthylène qui permet de protéger la plaque lors des différentes phases de stockage, manutention, transformation et découpe jusqu’à la livraison chez le client qui n’aura plus qu’à dépelliculer le film.
Classement au feu
Il existe différents types de classement au feu comme :
- le classement français qui classifie par M l’inflammabilité à la température et F la propagation de fumée. Les chiffres 0/1/2/3/4 déterminent le degré d’inflammabilité du matériau et sa performance, 0 étant la meilleure.
- le classement européen selon le système Euroclasses (A1 à F) dès lors que le marquage CE du produit est entré en vigueur pour les matériaux de construction (selon NF EN 13 501-1)
- le classement américain UL (Underwriters Laboratories) qui est le plus répandu et le plus utilisé.
Il détermine l’inflammabilité d’un polymère plastique. Il faut spécifier si le matériel plastique est additionné avec un retardateur de flamme.
Le premier essai HB détermine l’inflammabilité d’un polymère. L’essai VO, V1, V2 détermine le degré d’autoextinguibilité du matériau.
UL94 HB : Horizontal Burning – Brulure horizontale
Il consiste à mesurer le temps dans lequel l’éprouvette du matériau plastique avec une épaisseur spécifiée et montée horizontalement continue à bruler après avoir été mis sous la flamme d’un bec Bunsen pendant 30 secondes.
Selon la norme UL94 HB, le matériau est classifié HB quand l’éprouvette d’une épaisseur de 3mm brule avec une vitesse maximum de 76 mm/min.
S’il brule avec une vitesse inférieure à 40mm/min, il est alors classifié UL94 HB40.
UL 94 VO / V1 / V2 : Vertical Burning – Brulure verticale
Il consiste à mesurer le temps dans lequel l’éprouvette du matériau plastique avec une épaisseur spécifiée et montée verticalement continue à bruler après avoir été mis sous la flamme d’un bec Bunsen pendant 10 secondes.
Selon la norme UL94, le matériau est classifié V0 quand la flamme s’éteint dans 10 secondes sans égouttement.
Selon la norme UL94, le matériau est classifié V1 quand la flamme s’éteint dans 30 secondes sans égouttement.
Selon la norme UL94, le matériau est classifié V2 quand la flamme s’éteint dans 30 secondes avec égouttement.
Recyclage :
Soucieux des problématiques environnementales et acteur d’une politique de développement durable, CYTEC intègre ces questions dès la conception des produits en promouvant la transformation de matières issues de matières recyclées.
CYTEC propose à ses clients, et conformément à leurs attentes, une solution de recyclage des plateaux thermoformés après usage grâce à une zone de recyclage, de broyage et de re-extrusion directement sur notre site de production.
Domaines d’applications :
Les domaines d’applications sont divers et variés comme par exemple :
- AERONAUTIQUE
- AUTOMOBILE
- VEHICULE DE LOISIRS et SANS PERMIS
- VEHICULE AGRICOLE et INDUSTRIEL
- FERROVIAIRE
- NAUTISME
- MEDICAL
- ROBOTIQUE
- AGROALIMENTAIRE
- SANITAIRE
- MOBILIER URBAIN
- BATIMENT
- DIVERSES INDUSTRIES
- PLV (Publicité sur Lieu de Vente)
- EMBALLAGE
- MANUTENTION