Principe du rotomoulage
Le principe du Rotomoulage est né à la fin du 19e siècle (sous une forme mécanisée, car il n’est pas exclu que le principe ait été utilisé sous des formes plus précaires bien avant). Basé sur la rotation selon 2 axes perpendiculaires, les premières machines à manivelle furent utilisées pour la coulée d’objets creux en cire. Peu après, ce même principe trouva des applications dans la fabrication d’œufs en chocolat, puis de personnages tels que le Lapin de Pâques ou le Père Noël. Ce n’est qu’au milieu de 20e siècle, avec l’apparition et le développement des polymères, que fut introduit la fonction de chauffage du moule. Les premiers essais furent probablement réalisés avec des flammes chauffant le moule lors de sa rotation, puis rapidement apparut la technique consistant à chauffer le moule dans un four.
Dès lors, le polymère sous forme de poudre est déposé dans un moule froid. Le moule est ensuite fermé à l’aide de vis, de sauterelles ou autres systèmes mécaniques. Mis en rotation selon les 2 axes perpendiculaires, le moule est ensuite acheminé dans un four, où sa rotation se poursuit durant sa montée en température. Vers 200 degrés, la poudre de polymère se ramollit et se transforme en un liquide visqueux similaire à du miel coulant. Ce liquide visqueux, sous l’effet des rotations, vient tapisser la paroi intérieure du moule.
La phase suivante est le refroidissement. Tout en poursuivant les rotations du moule, ce dernier démarre son refroidissement, soit par convection naturelle, par ventilation ou par pulvérisation d’eau. Sous l’effet du refroidissement, le polymère se fige, il ne reste plus qu’à le démouler après avoir ouvert le moule.
Le rotomoulage et ses différentes étapes :
Coloration de la poudre :
- La poudre de matière plastique est colorée par adjonction de pigments
- L’étape de coloration est réalisée à l’aide d’un turbomélangeur, d’une bétonnière ou par compoundage.
- Pour un mélange intime du colorant et de la matière plastique, le compound est la solution la plus fiable. Il s’agit d’une méthode de mélange à chaud, où le plastique est malaxé avec le colorant dans une vis de compoundage. C’est aussi la technique qui conduit à une profondeur de la couleur la meilleure.
- Le turbomélangeur est une solution faisant appel à l’action mécanique des pales sur la matière, mais aussi l’action thermique due aux frottements durant le process.
- La bétonnière est la solution la plus simple, la moins onéreuse, et qui donne des résultats très satisfaisants pour 80% des applications.
- Le dosage de la matière colorée est réalisé par pesée, il correspond au poids de matière mis en œuvre dans le moule (selon le poids final souhaité pour la pièce)
Disposition de la matière dans le moule, fermeture du moule de rotomoulage :
- La matière préalablement colorée et dosée est versée dans le moule au moyen d’un contenant adapté (ou autre dispositif). Cette opération requiert du soin de la part de l’opérateur, pour laisser propres les zones de plan de joint.
- L’opérateur ferme le moule. Certains moules sont dotés de sauterelles, d’autres de vis. La conception de l’aspect ergonomique du moule est particulièrement importante pour la productivité ; chaque moule nécessite une réflexion particulière pour la conception de sa fermeture.
- Un test de rotation peut être effectué avant d’envoyer le moule dans le four, pour contrôler l’absence de fuites
Chauffage du moule
- Le chauffage du moule est obtenu dans un four, tout en conservant les rotations selon les 2 axes.
Refroidissement du moule
- Le refroidissement du moule est relativement lent pour éviter un choc thermique trop important sur l’outillage, et pour limiter les tensions dans la matière. C’est pourquoi il est généralement réalisé par simple ventilation, ou par ventilation accompagnée de pulvérisation d’eau.
Démoulage
- Ouverture du moule, puis extraction de la pièce rotomoulée.
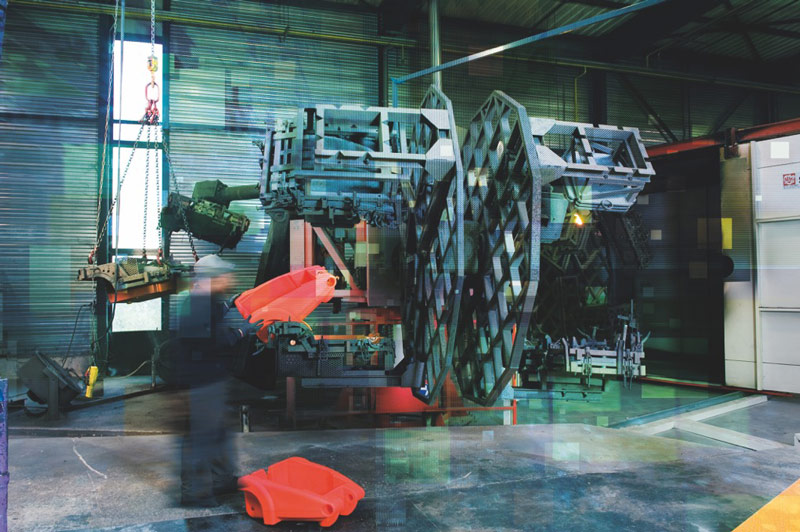
Le rotomoulage et ses avantages
Le rotomoulage présente de nombreuses particularités lui conférant des avantages techniques et économiques pour de nombreuses configurations de pièces. Il est adapté aux petites et moyennes séries, car les temps de cycle sont relativement longs
- le rotomoulage rend la fabrication de pièces creuses très simple, car il s’agit de son principe même.
- le rotomoulage admet des conceptions de pièces avec des formes parfois très complexes
- une pièce creuse pouvant être découpée, il est aisé de concevoir des pièces « ouvertes » réalisées par rotomoulage suivi d’une découpe.
- l’adjonction d’inserts métalliques et d’autres accessoires est très courante.
Les moules de rotomoulage
- les premiers moules de rotomoulage étaient en tôle formée par chaudronnerie, puis soudées entre-elles. Cette technique est toujours utilisée pour des pièces présentant des formes relativement simples, et pour des pièces de très grandes dimensions (quelques mètres dans chaque dimension)
- aujourd’hui de nombreux moules de rotomoulage sont en aluminium, soit une fonderie d’aluminium polie, soit une fonderie d’aluminium ré-usinée, soit sont usinés directement dans des blocs d’aluminium.
- les moules de rotomoulage sont souvent compétitifs par rapport à des techniques telles que le soufflage, l’injection.
- l’état de surface du moule (dans sa partie moulante) s’imprime sur celui de la pièce. Ainsi un moule poli donnera lieu à une pièce rotomoulée lisse, un moule grainé donnera lieu à une pièce grainée.
Les pièces complexes réalisées par rotomoulage
Au fil du temps, les techniques et astuces entourant la fabrication des moules de rotomoulage se sont perfectionnées, aboutissant aujourd’hui à la possibilité de formes très complexes et de dimensions très grandes.
Les applications pour les pièces rotomoulées sont multiples. Parmi les plus souvent rencontrées, on peut citer.
- des réservoirs de grande taille destinés à l’assainissement dans le domaine de l’habitat (fosses septiques, récupération d’eau de pluie, réservoir de fuel)
- des réservoirs de formes complexes (réservoirs embarqués sur des machines agricoles, des machines de TP, des bateaux, des camping-cars)
- des pièces de signalisation routière (musoirs, séparateurs de voies, cônes, supports de panneaux, feux de chantier)
- des capots de véhicules spéciaux (gardes boue, toitures, habillages intérieurs, pare-chocs,…)
- des capots de machines (machines de travaux publics, agricoles, nettoyage industriel)
- des pièces design : mobilier urbain, sapin Modulo et personnage Manelo commercialisés par Naturplas
- des calages pour le transport de pièces mécaniques (utilisation dans le secteur automobile)
- des flotteurs et bouées maritimes (pontons, bouées de signalisation,…)
- les loisirs (canoés kayak, barques…)
Les qualités d’un polymère destiné au rotomoulage
Les plastiques utilisés pour le rotomoulage doivent répondre à un certain nombre de critères tels que :
- La fluidité à sec : c’est la capacité de la poudre à se déplacer dans le moule sous l’effet de la rotation et de la gravité. La finesse du grain est une caractéristique importante.
- La fluidité à chaud : une fois chauffée, la poudre se transforme en un liquide visqueux similaire à du miel coulant. Selon que le moule présente des formes saillantes, des angles, des zones peu accessibles durant la rotation, la fluidité doit être plus ou moins grande. Une trop grande fluidité aura un effet néfaste sur la régularité des épaisseurs, et pourra s’écouler du moule durant la phase de chauffe. Une trop faible fluidité laissera apparaître des zones mal remplies, des bulles, des trous.
- La tenue aux UV : des additifs introduits dans la matière conduisent à une tenue satisfaisante aux UV
La liste des caractéristiques
Ci-dessous, la liste de quelques caractéristiques souvent évoquées pour les pièces rotomoulées :
- Densité
- Dureté Shore
- Température de ramollissement
- Indice de fluidité
- Coefficient de dilatation thermique
- Retrait
- Mesure de propriétés mécaniques
- Résistance au choc
- Résistance à la rayure
La recyclabilité
La plupart des matières transformées par rotomoulage sont recyclables. Après broyage puis micronisation, elles peuvent être à nouveau rotomoulées.
Les différents polymères utilisés pour le rotomoulage
Ci-dessous, une liste de matières pouvant être transformées par rotomoulage
- Le polyéthylène
- Le PVC (Polychlorure de vinyle)
- Le polypropylène
- Les polyamides
- Le polycarbonate
- De nouvelles matières issues de végétaux voient le jour (PLA).
Les évolutions de la technique de rotomoulage
Traditionnellement le rotomoulage était une technique presque artisanale, qui requérait un taux de main d’œuvre élevé. Le rotomoulage offre la possibilité, avec des moyens modestes, de réaliser des pièces complexes et de grandes dimensions. L’intervention humaine dans la conduite des machines aboutit à un taux de rebuts parfois élevé, la difficulté de recruter du personnel se renforce, le coût de la main d’œuvre progresse, tout ceci a conduit à des réflexions sur l’avenir du rotomoulage à et son automatisation. Avec l’aide de robots anthropomorphiques, il devient possible d’automatiser certaines tâches, voire d’automatiser complètement les processus de fabrication d’une pièce rotomoulée.
Cette réflexion s’étend à la conception des moules, particulièrement avec le concept de chauffe et/ou de refroidissement intégré au moule (par circulation d’un fluide chaud et/ou froid). Ces avancées technologiques, particulièrement adaptées aux moyennes séries, connaissent une progression lente, mais vont très probablement prendre une place plus importante à l’avenir.